The demand for wire ropes has been escalating in recent years because of the many advantages they bring. Brainchild of Wilhelm Albert, a German Mining Engineer, the different kinds of wire ropes are now used across different industries including mining, construction, oil & gas, logging and many more. The initial wire ropes comprised of six twisted strands of wire around a hemp rope core mainly in different directions to achieve the best stability. With the improvements in technology, wire ropes have become more sophisticated and durable. Back in 1800s, wire ropes were made out of wrought iron instead of steel.Wire ropes have become the most preferred choice in recent times because of their unbelievable tensile strength. Most importantly, because of the friction between the wires and strands, there are fewer chances of anything going wrong. There are essentially three main components of a wire rope namely wires, strands and a core. The wires are carefully selected from different grades of steel to offer maximum strength. Wire ropes come in different types each having its specific use. These also come in different classifications. For instance, a 6×25 wire rope means it consists of a six-strand rope with each strand having 25 wires. One should figure out the requirements properly before buying these. Discussed below are some of the most common types of wire ropes available in the market along with their applications. Standards Wire Ropes Some of the most common types of standard wire ropes include the class wire rope and alternate lay wire rope. The former is used in places where wear and abrasion frequently occur. These large wire ropes have an amazing ability to withstand wear. However, they are generally not meant to endure the bending stress. Also known as reverse lay, the alternate lay wire ropes offer an extra lang-lay flexibility apart from structural stability. To improve abrasion resistance, these are prepared with large outer wires. Unlike class wire ropes, these can easily withstand bending stresses. Alternate lay wires are largely meant for winding applications where crushing and abrasion is quite common.Hoist Wire RopesAlso known as elevator ropes, these are commonly used on lifts & elevators in merchant vessels. Hoist ropes generally have a steel or fibre core with 6 or 8 stands. For the elevator wire rope construction, lang lay and regular lay are used. Each of these has its own benefits. For instance, the lang lay helps enhance a wire’s fatigue life whereas the regular lay offers resistance against crushing.Rotation Resistant Wire RopesIf you are looking out for ropes that offer rotational stability, go for rotation resistant wire ropes. These contra helically laid ropes are different than the standard wire ropes and therefore one should be extremely careful in using time. Further, using a swivel with this kind of wire rope must be dealt with absolute caution. Avoid any practice that might cause the load to unbalance between the inner and outer layers of strands. Similar to other types of ropes, these too come in various classifications. For instance, 8×19 classifications are generally used for hoisting unguided loads with a multipart or single part line. Next, SFP 19 rotation resistant wire ropes offer unmatched fatigue and abrasion resistance. It is mostly used as a long fall on offshore pedestal cranes and crawler cranes.Specialized Wire RopesThe use of wire ropes differs from industry to industry. Therefore, there are a specific set of wire ropes available for special uses in – • Power and communication pulling lines• Soil compaction• Water well drilling• Foundation drilling• Bridges, stadiums (structured wire ropes)• Cableways• Power scaffoldingMooring Wire RopesThese types of wire ropes are mainly used by oil and engineering companies. Mooring operations need a thoughtful planning in order to create safe working conditions for workers. Mooring wires are designed with robust capabilities to withstand external forces including fatigue, wear and abrasion. These make it possible for the crew to work in a safe environment. These wires are often designed with a larger diameter to reduce corrosion damage and improve abrasion resistance. Mooring wire ropes need to be handled with great caution to avoid injury.Cargo WiresMainly used in cargo lifting appliances and gantries, the strength of cargo wires varies depending on the crane design and lifting appliance. For instance, if you are using these wire ropes in a ship’s crane with 20 to 60 tonnes of SWL, the wire has to have a breaking strength of at least 4 times the maximum duty load.Often the types and classifications of wire ropes that are available in the market are overwhelming. Therefore, figure out your requirements to choose one of the most appropriate Wire Rope Slings for your business.
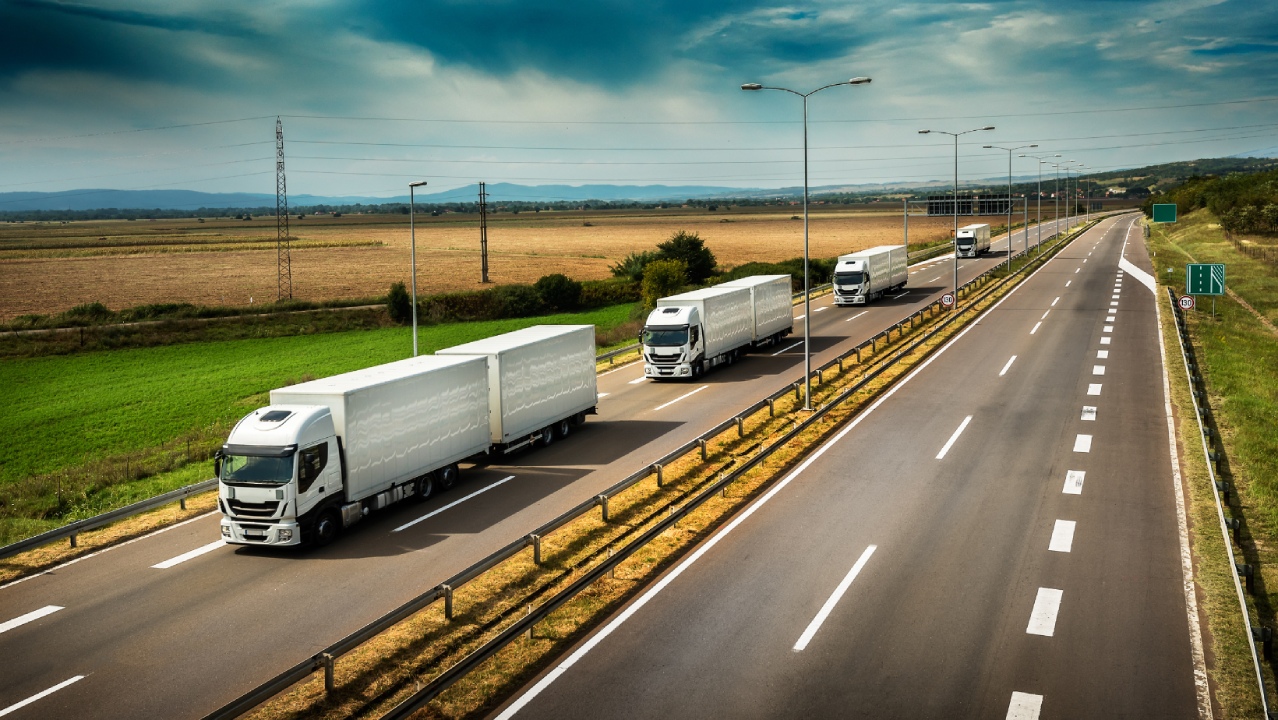